Protect Roll Products
Protect Roll Products with Custom Pallet Design
Protecting rolled products from damage is one of the more challenging jobs for unit load material handling.
If you work with heavy rolls of foil, film, paper, plastics or other high-value material, you know that damage during transport or storage can make the product unusable. That's a costly mistake no one wants to make. Custom solutions like the ones we show below can help prevent callbacks.
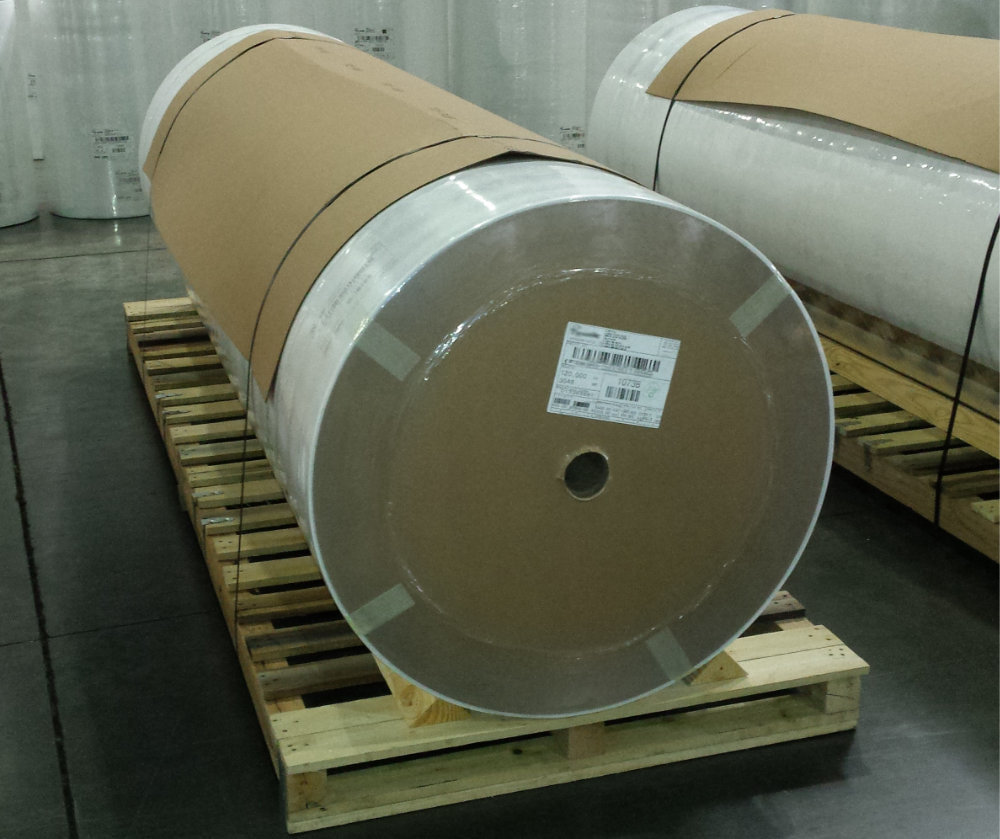
This custom wooden roll pallet supports the entire length of cylindrically-shaped product.
Shipping Roll Products
To develop a better protection system for transporting factory rolls, everything from the roll properties to customer requirements must be considered. A minor dent is not so minor when it causes thousands of dollars in loss. Equally cringe-worthy is a load that shifts during transport and causes product to open or roll away.
There are three main ways to ship rolled products:
Vertical Rolls
Vertical Rolls put the least stress on a pallet or platform. This solution is best suited for rolls that can handle being shipped in an upright position. Advantages include lower-cost pallets and minimal unitizing to keep the roll(s) secure on the pallet.Cradle Supports
Cradle supports work best when rolls can withstand pressure from the pallet or packaging and can ship in a horizontal position. This option requires more pallet support and some type of "cradle" to hold the roll secure. Made from wood, plastic, foam or paper, cradles can be permanently attached to the pallet or added at time of shipping.Suspended Rolls
When rolls cannot withstand pressure from the pallet, they are suspended. Roll cores are typically attached to header boards at each end to keep the roll suspended above the pallet. While this is the most protective shipping method, the strength and stiffness requirements for the pallet are much greater. Extra nails, wider boards at tine tips and other securement reinforcements help prevent any part of the pallet from touching the roll during handling.
Suspending rolled product between boards and above the pallet prevents impression damage from handling pressure.
Maximize Protection while Minimizing Cost
If you are experiencing too many callbacks due to roll damage, it may be time for a change. And not just for damage control. Shifting over to a better roll pallet design can also save time by streamlining the palletizing process. Delivering products on time and in pristine condition saves money plus offers a competitive advantage.
If the product is not highly susceptible to damage, placing rolls in a vertical position on the pallet often saves money.
Reduce Rolled Product Transit Damage
How many callbacks are you getting for rolled product damage? Tell us about the damage you're experiencing below and Let's connect to find the best packaging solution to ship and secure your valuable rolls.
Updated: 12/12/2024 | Published: 6/14/2018
by John Clarke
on Case Studies